Сера, по своей сущности — это термопласт. То есть, композиты, выполненные на основе данного вещества, включая и серные бетоны, являются термопластами. Конструкции, изготовленные из таких смесей, обладают высокими теплоизоляционными свойствами, прочностью, они устойчивы к химическому воздействию кислот, солей, масел и пр. При необходимости, учитывая проектные требования, прочность изделий может быть повышена методом введения в состав растворов (до 7%) стекловолокнистой фибры.
Серобетоны отличаются рядом положительных качеств, в сравнении с другими аналогичными материалами.
Это:
- период набора прочности, связанный только с остыванием смеси;
- низкая цена исходных компонентов;
- возможность вторичной переработки материалов, что позволяет организовать безотходное производство изделий;
- стойкость к воздействию агрессивных сред:
- способность твердения смесей при достаточно низких температурах;
- за счет высокой скорости схватывания — быстрая оборачиваемость форм;
- низкая электро- и теплопроводность;
- водонепроницаемость;
- повышенная морозостойкость;
- высокая износостойкость.
Результаты исследований показывают, что серные композиты по плотности, показателям пористости и водопроницаемости, существенно превосходят классические цементные растворы. Например, водонепроницаемость конструкций, изготовленных из этих материалов, в 10–20 раз выше, чем у аналогичных изделий из тяжелого бетона.
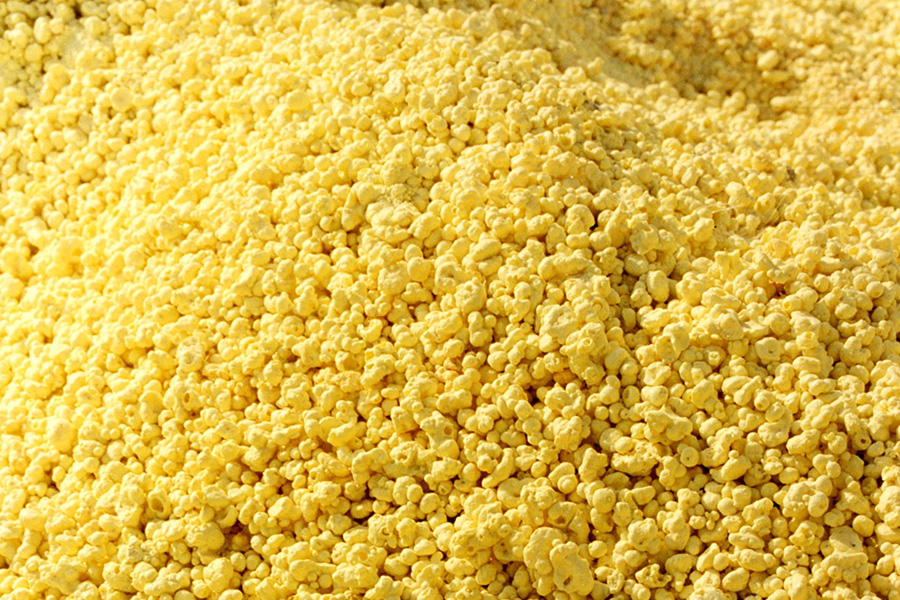
Еще одним важным фактором, является износостойкость покрытий, которая почти в пять раз выше значений эксплуатируемых изделий на цементных вяжущих.
Однако, невзирая на такие положительные характеристики, отдельные недостатки серобетона могут отрицательно сказаться на широком его использовании:
- Высокая температура (140°С) для приготовления смесей.
- Высокая цена установки для выпуска изделий (10–12 млн).
- Высокая токсичность производства (выделение сероводорода).
- Низкая термостойкость (+90°С).
Серные бетоны по своему составу относятся к разряду специальных бетонов. Общие технические нормы и требования, предъявляемые к смесям и изделиям их них, перечислены в предварительном национальном стандарте — ПНСТ105-2016.
Условия настоящего стандарта необходимо соблюдать при проектировании и составлении технологической документации, а также руководствоваться при проведении строительных работ и определении качества готовых конструкций.
Учитывая среднюю плотность, композиты подразделяются на следующие категории:
- особо тяжелые — плотность >2,8 г/см3 (СбС О), марки D2500 и выше;
- тяжелые, со средней плотностью 1,8–2,8 г/см3 (СбС Т), D2000—D2500;
- легкие — <1,8 г/см3 (СбС Л), в пределах D800—D2000.
По показателям удобоукладываемости делятся на группы:
- жесткие (Ж);
- подвижные (П);
- литые (Л).
Условное наименование серобетонного раствора стандартного качества состоит из аббревиатуры: группа подвижности, класс прочности, и по необходимости может указываться морозостойкость, средняя плотность и водонепроницаемость.
Серобетоны используются в элементах конструкций жилых зданий и промышленных сооружений, в процессе эксплуатации которых необходимы высокие значения атмосферо- и морозостойкости, непроницаемости, повышенной устойчивости к воздействию агрессивных сред.
Наибольшее распространение применение серобетона получило при производстве следующих мелкоштучных изделий и конструкций:
- Устройство дорожных покрытий (серный асфальтобетон).
- Изготовление элементов сборных автодорожных покрытий (плиты, бортовые камни, торцовые шашки, дорожные ограждения, тротуарная плитка).
- Элементы зданий, которые в процессе эксплуатации подвергаются воздействию солевой среды (фундаменты, полы, сливные лотки и др.).
- Инженерные конструкции (канализационные трубы, коллекторные кольца, очистные сооружения).
Технология изготовления серобетона основана на том, что вместо воды и портландцемента, для приготовления смесей в качестве связующего компонента, используют техническую серу (20–40%) или серосодержащие отходы промышленных производств. В роли крупного заполнителя для тяжелого бетона выступает искусственный или природный щебень пористой или плотной структуры. Максимальная величина зерен не должна превышать 40 мм. Для особо тяжелых смесей необходимо применять металлическую стружку или свинцовую дробь.
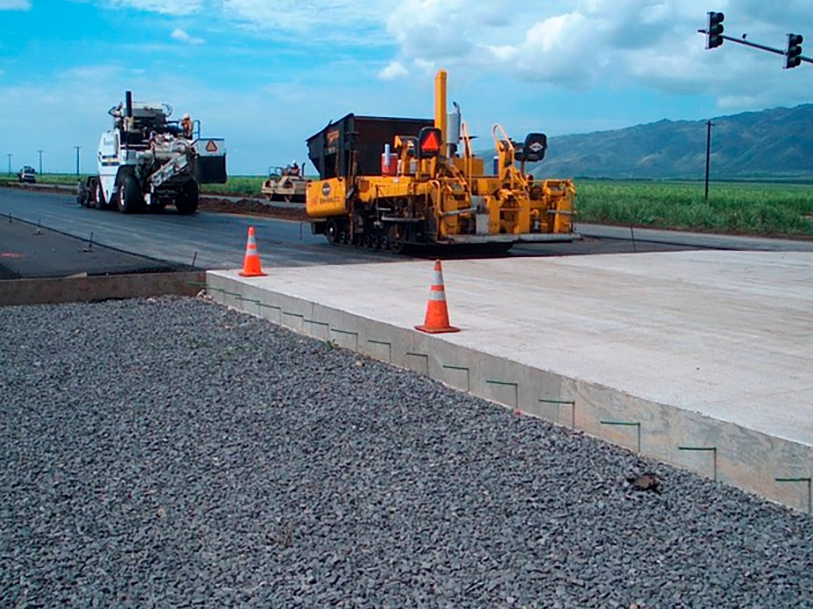
При производстве легких бетонов используют пористые заполнители (ГОСТ 32496-2013):
- керамзитовый гравий;
- аглопоритовый щебень;
- шунгизитовый гравий;
- металлургические шлаки.
В качестве мелкозернистых заполнителей применяют природный кварцевый песок, который по своему составу может быть:
- природный обогащенный;
- природный фракционированный;
- дробленый;
- дробленый фракционированный.
Различные типы мелкого и крупного заполнителя употребляются, в зависимости от вида и назначения изготавливаемых элементов конструкций и условий их использования.
В роли инертных наполнителей (см. табл.), служащих структурообразователями, выступают тонкодисперсные материалы с величиной зерен менее 0,15 мм, в том числе:
- андезитовая мука;
- маршалит;
- кварцевая мука;
- диабазовая мука;
- графитовая пудра;
- зола-унос и другие минеральные порошки.
Отдельной строкой, в списке заполнителей, находятся материалы для армирования серных бетонов — фибры. В результате такого подхода к производству изделий, получаются прочные и долговечные конструкции из фибросеробетона. В качестве фибр применяют органическое или неорганическое волокно в количестве 5–7% от общего объема используемой серы. Дисперсное армирование производится волокнистым материалом в виде связанных в пучок нитей, предварительно пропитанных клеящим составом, например, акриловой, эпоксидной или полиуретановой смолой. Рекомендуется применять фибры не длиннее 3–5 см с диаметром волокон 150–350 мкм. Сера в пределах температур 15—20°С представляет собой твердое кристаллическое вещество. Обладает низкой тепло- и электропроводностью, а также не растворима в воде. Данное вещество способно образовывать соединения практически со всеми органическими и неорганическими химическими элементами. Температура плавления материала 120°С. А если довести температуру расплавленной серы до 445°С, она закипает. В твердой фазе сера по своим качествам — хрупкий материал. В результате чего, затвердевший расплав не обладает удовлетворительной прочностью. Поэтому, для получения качественных композиций на основе серных вяжущих применяют только модифицированные вещества, обладающие аморфно-кристаллической структурой, существенно повышающей механические свойства изделий.
Модифицирующие добавки вводятся в момент приготовления расплава серы в зависимости от эксплуатационных требований и принятой технологии производства. Количество той или иной присадки может составлять 1–10% от общего объема серного концентрата.
По своему функциональному назначению лигатуры можно разделить на несколько категорий:
- пластификаторы (каучук, стирол, нефтеполимерные смолы, парафин и др.);
- стабилизаторы (поливинилхлорид, хлорид цинка и пр.);
- антипирены (сульфид мышьяка, треххлористый фосфор);
- антисептики (нафталин, тимол).
Композиция, видоизмененная специальными присадками, получила наименование: полимерная сера. Технологической особенностью производства серных бетонов, является метод их получения по, так именуемой, «горячей» технологии. При этом, в процессе производства бетона все компоненты смеси нагреваются до 150°С. При таком режиме сера переходит в жидкое состояние (температура плавления 120°С). Расплав серы в растворе выполняет все функции вяжущего, определяющего главные технологические параметры композиций (удобоукладываемость, подвижность). Жизнеспособность смесей в горячем состоянии практически не ограничена.
Одностадийное перемешивание вмещает в себя одну операцию:
- в работающий смеситель постепенно вводят необходимое количество разогретых до 150°С песка и щебня;
- добавляют наполнители (порошок, муку);
- загружают расплав серы;
- тщательно перемешивают до получения готовой однородной смеси.
Время всего технологического цикла занимает 8–10 мин. При двухстадийном изготовлении, отдельно готовят серную мастику и бетонную смесь (два этапа). Затем, всю эту массу соединяют в смесители и перемешивают.
Готовая смесь загружается либо в бункер-накопитель, либо непосредственно в подготовленные для изделий формы.
Производство изделий включает следующие операции:
- подготовка форм;
- установка закладных деталей и арматурных каркасов:
- разогрев форм до необходимой температуры;
- укладка готовой смеси;
- уплотнение смеси;
- остывание;
- распалубка.
Уплотнение растворов в формах производится на виброплощадках. Продолжительность вибрирования зависит от сложности изделия, и обычно составляет 1–2 мин. Критерием служит прекращение появления пузырьков воздуха на поверхности. Распалубка готовой продукции выполняется при температуре затвердевшего изделия не выше 40°С. После этого, проводится выдержка изделия без опалубки до полного остывания. Затем, изделие транспортируют на склад готовой продукции. Рассмотренная технология изготовления серобетона не предусматривает приготовление своими руками данного вида материала в условиях строительной площадки. Допускается вариант самостоятельного производства изделий в коммерческих целях, при использовании специальных мобильных установок.
В статье используются материалы из источника:
https://beton-house.com/vidy/specialnye/serobeton-1022