По мнению специалистов полимерная добавка для битума позволит повысить прочность дорожного полотна в три раза, а затраты на производство - снизить за счет доступных процессов и компонентов. Результаты работы были опубликованы в материалах всероссийской научно-практической конференции «Химия. Экология. Урбанистика», а также в журнале «Вестник ПНИПУ. Химическая технология и биотехнология».
С каждым днем транспортная инфраструктура разрастается и развивается, поэтому возрастают и требования к износостойкости и долговечности асфальтобетонного покрытия. Ежегодно на решение вопроса плохих дорог и их прочности в мире тратится около 1,6 трлн. тонн асфальта, однако это не помогает привести дорожные настилы в пригодное на долгие годы состояние.
Сегодняшние дороги и в России – не идеальные. Чтобы увидеть масштаб проблемы, достаточно зайти в разделы «Авто», «Дороги», «Социальные новости» или «Общество» в различных СМИ. Например, в апреле этого года, по сообщениям в редакцию «Блокнот Волгограда», местные жители жаловались на то, что из-за плохих дорог у них попросту ломаются машины, а доехать до соседних населенных пунктов в больницу, школу или магазин в принципе не представляется возможным.
Проблема плохих дорог заключается в основном компоненте асфальтобетона – нефтяном битуме, добавки в котором стали менее надежными компонентами для строительства дорог.
Горная смола для городских дорог
Асфальт – это горная минеральная смола, которая представляет собой черное или черно-бурое блестящее вещество. Его чаще всего используют для устройства покрытий на автомобильных, аэродромных дорогах, и иногда называют асфальтобетоном – искусственным материалом, состоящим из щебня, песка, минерального порошка и битума.
Среди всех вариантов дорожного покрытия, асфальт оказался самым благоприятным – он менее шумный, чем булыжники или брусчатка, а его покрытие легко монтируется, моется и убирается. Также асфальт обладает нужной шероховатостью, хорошо держит разметку любого характера, и сразу же позволяет запустить потоковое движение автомобилей, в отличие от цементобетона, который становится прочнее лишь в течение 28 дней после укладки.
Битум, в свою очередь, является горной смолой – нефтепродуктом, результатом выветривания нефти. По сути, битум – основа асфальта, потому асфальт можно назвать одним из его классов. Главная особенность битума – вяжущие, гидро-, газо-, электроизолирующие качества. Его стойкость к воздействию химических элементов, коррозии и других явлений обеспечивает широкое применение в качестве защиты различных сооружений и изделий. Чаще всего нефтяные вязкие битумы используются в дорожном строительстве, в асфальтобетонных составах; в них битум соединяет компоненты смеси: щебень, песок и минеральные элементы, сохраняя необходимые прочность и пластичность.
Земляная смола» для Тучкова моста
Битум считается одним из древнейших строительных и отделочных материалов, использование которого относится еще к эпохе неолита. Тогда «земляную смолу» применяли для скрепления наконечников копий и повышения влагоустойчивости посуды. Битум был также популярен в строительстве, архитектуре, бальзамировании и мумификации.
В начале XIX века улицы городов мостились булыжниками, но уже в середине столетия, во Франции, США и ряде других стран их стали делать из битумно-минеральных смесей. 1830-е годы стали знаменательными – именно тогда появился тротуар из асфальтобетонной смеси; ею покрыли парижский Королевский мост Руаяль. Лето 1839 года и в Санкт-Петербург дошли инновации – тротуары и часть Тучкова моста были также покрыты асфальтом.
Развитие дорожных сетей происходило бурно, поэтому для них нужно было находить все более прочные и модифицированные «асфальтовые решения». В 1876 году в США впервые применили литой асфальт с содержанием нефтяных битумов. В России изготовлением асфальта занимался инженер-архитектор Иван Буттац; асфальт добывали на Сызранском заводе, на правом берегу Волги с 1873 года.
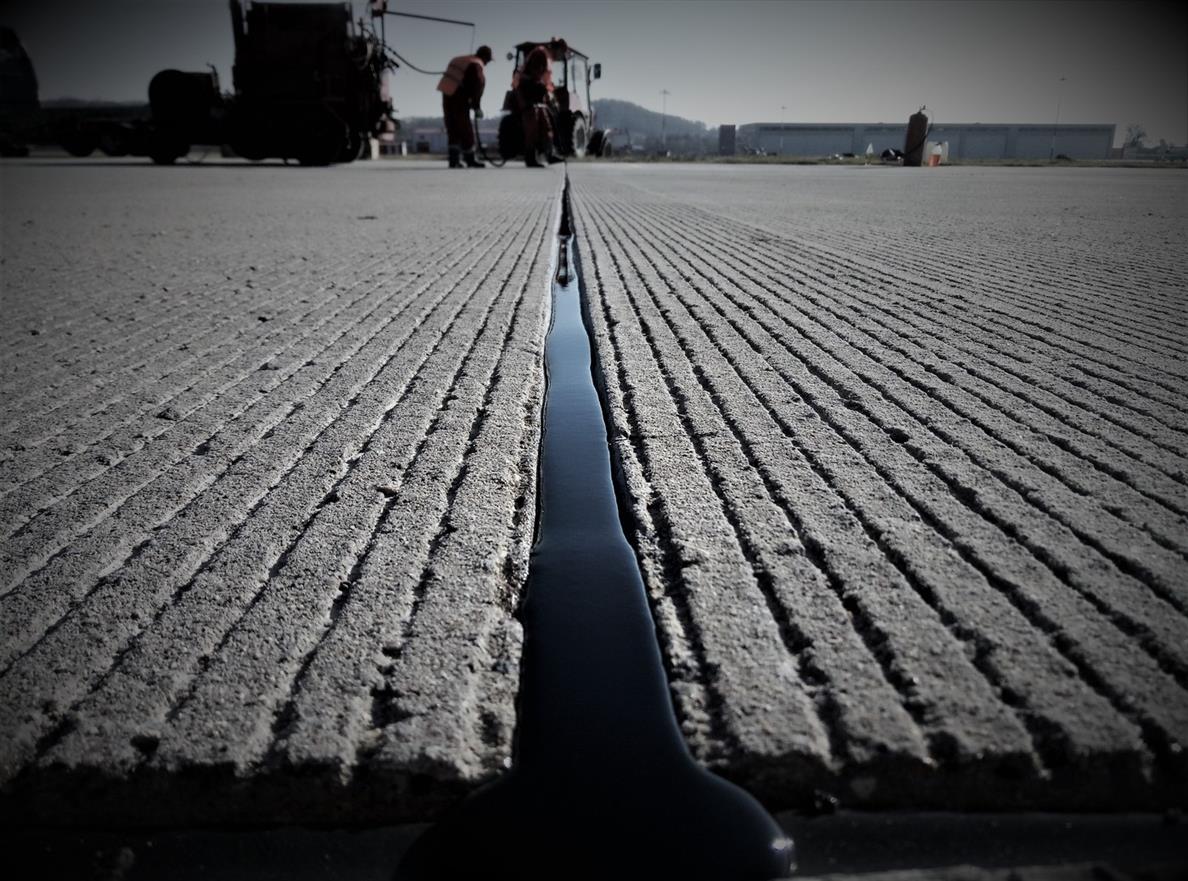
До 1900-х годов чаще всего использовался природный асфальт; он образовывался, когда сырые нефтяные масла пробивались сквозь трещины на землю, а ветер и солнце высушивали их, оставляя черный осадок. С открытием возможностей для переработки и модификации асфальта, а также популярностью автомобилей, дорожная промышленность не оставалась на месте. Так появился современный искусственный асфальт – он обладал всеми теми же качествами, что и природный, но был однородным, без каких-либо примесей.
Сырьем для производства битума для асфальта является нефть. Существует несколько способов получения битума, но самый широко используемый в дорожных покрытиях – окисление нефтяных остатков кислородом при высоких температурах. Основными факторами окисления становятся температура, расход воздуха и давление. Сегодня битумы получают благодаря окислению нефтяных остатков кислородом без катализатора при интервале температур в 180-300 градусов Цельсия на протяжении примерно 12 часов.
Из нефтяных скважин на нефтеперерабатывающие заводы поставляют сырую нефть, где ее впоследствии можно разделить на различные компоненты с помощью процесса дистилляции до других необходимых продуктов: асфальта, парафина, бензина, смазочного масла, керосина или дизельного масла.
Для мощения улиц и мостов асфальт прогоняют через дистиллят с помощью воздуха или тепла, испаряя масла и другие летучие вещества, чтобы получился твердый асфальтовый цемент. Для того, чтобы асфальт был быстротвердеющим, его нагретым смешивают с бензином, для среднего отверждения – с керосином, а для медленного отверждения – с остаточным маслом из раннего процесса дистилляции.
Также асфальт могут измельчить для получения порошкообразного вида. Чтобы добиться равномерных гранул, его прогоняют через много сит, а затем смешивают с дорожным связующим маслом и заполнителем для строительства тротуаров.
До недавнего времени в качестве связующего элемента в асфальтобетонных смесях, а также при выполнении дорожных работ и изготовлении строительных изделий люди использовали так называемые классические БНД – уже известные нам битумы нефтяные вязкие.
Сегодня рост интенсивности движения, нагрузок на дороги, климатические условия, ужесточение требований к материалам для строительства и ремонта дорог привели к тому, что БНД уже не могут выполнять свои функции в полной мере. Во-первых, при повышенных температурах они становятся мягче, образуя колеи, а при пониженных – твердыми и хрупкими, что провоцирует трещины. На восстановление дорог уходит много времени и денег, а местные жители города или улицы страдают из-за долгих ремонтных работ и невозможности быть мобильными. Это же заметили и ученые из Пермского политехнического университета.
Дело в том, что активное развитие транспортной инфраструктуры прямо пропорционально требованиям к прочности и долговечности дорожного покрытия – чем быстрее развиваются дороги, тем прочнее они должны быть. Да, дорогие модификаторы, вроде искусственного каучука, атактического полипропилена или окисленного битума хорошо справляются со своей работой. Они укрепляют битум, позволяют асфальту быть прочным при высоких и низких температурах, хорошо соединяют различные компоненты внутри асфальта для более прочной и долговечной службы. Однако, из-за важного недостатка этих модификаторов – естественного старения – на их поверхности начинают расти грибки, мхи и прочие биологически активные организмы, а сам материал может вздуваться, крошиться и выделять неприятный запах. Конечно, очистка асфальта помогает в этом вопросе, но дополнительные затраты на покупку средств для обработки поверхностей на основе медного купороса иногда ставят строителей в тупик. Именно поэтому дороги зачастую приходят в негодность раньше времени.
Специалисты из Пермского политеха решили взяться за модификацию битума. Нужны были добавки, которые продлевают срок службы битума за счет придания ему дополнительных свойств. Без таких добавок асфальт служил бы гораздо меньше. Нефтяной битум ученые решили модифицировать с помощью добавления различных полимерных добавок, но с небольшими изменениями – частично заменив дорогостоящие модификаторы на термопластичный полимер и убрав из процесса получения высококачественного битума процесс окисления.
Полимеры – это вещества с многократно повторяющимися структурными звеньями в молекулах: бывают природные – крахмал, целлюлоза, и синтетические – пластмассы, каучуки. Термопластичный полимер отличается своим свойством многократно размягчаться при нагревании и приобретать твердость при охлаждении. Термопласты хорошо набухают и отлично испаряются, а после растворения – возвращаются в твердое состояние. Есть у них и недостатки, например, низкая термоустойчивость, однако полистирол, один из полимеров группы термопластов, является очень прочным и обладает высокой теплостойкостью без деформаций.
Итак, заменив дорогостоящие модификаторы на термопластик, ученые получили высококачественные полимерно-битумные вяжущие – ПБВ или битум нефтяной дорожный вязкий, состав которого значительно лучше благодаря добавлению в него пластификаторов, которые увеличивают пластичность и эластичность, и адгезионных добавок, для лучшего сцепления поверхностей компонентов. Это обеспечивает высокую прочность и долговечность дорожного полотна. Таким образом, пермские ученые смогут даже импортозаместить зарубежные аналоги, используя полимеры отечественного производства.
Секрет дешевизны состоит в том, чтобы добавить в гудрон, остаток переработки нефти, смесь полимерных добавок, которая придает материалу эластичность, существенно расширяя его температурный интервал работоспособности. Пермские ученые рассчитали, при какой концентрации характеристики получаемого битума будут соответствовать современным нормативам, а также проверили, можно ли добавить в битум, помимо дорогих модификаторов, дешевый полиэтилен без потери качества.
«Добавление полимеров в неокисленные нефтепродукты не является принципиально новым подходом, однако приводит к значительному удорожанию себестоимости получаемого продукта из-за дорогих полимерных модификаторов. Наша разработка позволила заместить часть дорогостоящего полимера на сравнительно дешевый полиэтилен без существенной потери качества продукта», — рассказывает кандидат технических наук, доцент кафедры химических технологий ПНИПУ Антон Ширкунов.
Таким образом, замена процесса окисления на пермскую технологию упростит производство асфальта, предотвратит образование выбросов газов окисления, высокую токсичность и канцерогенные свойства. Как итог: улучшается экология на производстве и вокруг, а вместе с ней и дороги. Представители университета утверждают, что технология уже готова к внедрению и не требует значительных затрат на производстве.
В статье используются материалы из источника:
https://saint-petersburg.ru/m/science/redaktor6/396159/