Были изучены различные методики уплотнения асфальтобетонных смесей, и, как следует из табл. 2, объемная плотность по Маршаллу для тяжелых условий получилась самая незначительная, в отличие от компактора и гиратора. Образцы на компакторе и на гираторе были подвержены испытанию на колею. Результат по колее у образца, уплотненного на гираторе, лучше на 42%, при практически одинаковой плотности образцов. Эти данные говорят о том, что различные методы уплотнения оказывают сильное влияние на итог проектирования одной и той же смеси. Анализ полученных данных показал следующее:
- тип А, который мы раньше при меняли, при правильном методе подбора может иметь такие же качественные характеристики, как и А16ВТ;
- новые стандарты позволяют проектировать смеси наиболее правильно и с требуемыми характеристиками;
узкие фракции щебня позволяют поддерживать в смеси правильное соотношение каркасообразующих
материалов; - результаты определения средней глубины колеи разнятся при формовке на компакторе и гираторе, при практически одинаковом содержании воздушных пустот;
- объемная плотность асфальтобетона при уплотнении по Маршаллу 75 ударами ниже, чем после компактора и гиратора.
Данный метод проектирования отвечает и ГОСТ Р 58401, и ГОСТ Р 58406, методики испытаний асфальтобетонной смеси одинаковые. Таким образом, на асфальтобетонном заводе ничего менять не придется. Важно обратить внимание на то, что при проектировании асфальтобетонной смеси по ГОСТ Р 58401 отличие от ГОСТ Р 58406 состоит в следующем: смесь нужно проектировать при содержании воздушных пустот 4,0±0,3% (допускается по согласованию с заказчиком SMA проектировать при 3,0%). Кроме того, учитывается отношение «пыль – вяжущее»; вместо уплотнителя Маршалла используется гиратор. К основным отличиям следует отнести и разные требования к одним и тем же показателям (колея, коэффициент водостойкости), а также использование битума марки PG.
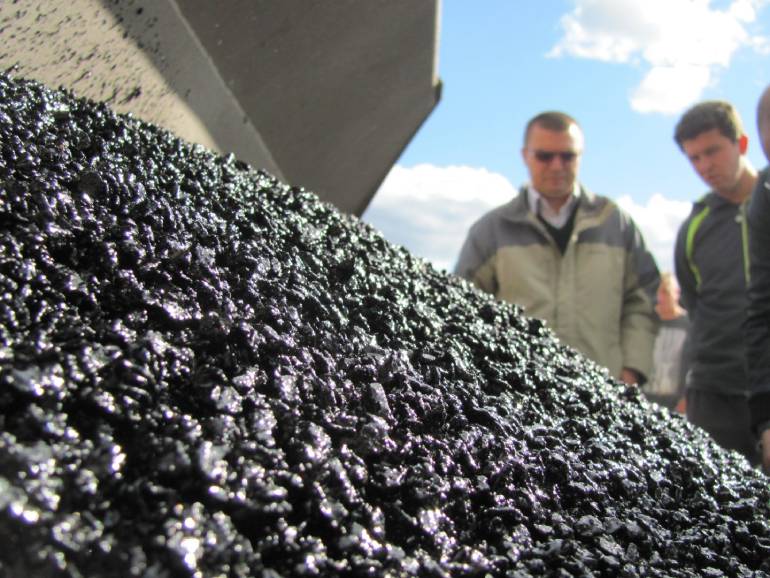
Современные асфальтобетонные заводы, имеющие пять и шесть горячих бункеров-накопителей, позволяют использовать основные фракции каменных материалов и с высокой точностью их дозировать благодаря
современным блокам дозаторов. Это в итоге позволяет получать смеси по ГОСТ 58401 и ГОСТ 58406. Они вписываются не только в допустимые пределы ГОСТа, но и в рецепт, разработанный в лаборатории, что гарантированно позволяет получать стабильную и качественную смесь.
К сожалению, морально устаревшие заводы с четырьмя накопителями не могут похвастаться точностью дозирования и не позволяют использовать широкий диапазон основных фракций. Это в результате приводит к использованию широких фракций, из-за чего теряется стабильность производства. При изготовлении смеси также очень важно контролировать ее на соответствие рецепту, в чем очень хорошо
помогает асфальтоанализатор. Результат можно получить в течение часа, что позволяет в случае необходимости провести корректировку прямо на заводе.
Следующим шагом является определение максимальной плотности смеси. Так, если объемы выпускаемого продукта большие, данные испытания необходимо проводить несколько раз в смену, поскольку этот показатель может меняться, влияя, в конечном счете, на приемку покрытия из-за неправильных данных по воздушным пустотам. Помимо контроля смеси, необходимо периодически определять на реометре температуру битума, при которой будет производиться смесь на заводе, а также температуру, при которой будет осуществляться укладка асфальтобетона на дороге. Если же в процессе эксплуатации или укладки возникают проблемы, всегда можно изучить вяжущее, которое было использовано, с помощью ротационного испарителя.
Данный принцип производства и укладки описан для асфальтобетонных смесей, запроектированных по методологии Маршалла. Его отличие от метода объемного проектирования невелико: разница лишь в проектировании смеси и уплотнителе. В процессе укладки особую роль играет температура укладки и режим уплотнения. А ведь еще три года назад не было верхнего предела по уплотнению. Дорожники закатывали асфальт до состояния, когда щебеночный каркас начинал ломаться внутри. По нормативам уплотнение получалось всегда очень высокое, однако в ходе эксплуатации это приводило к разрушению покрытия быстрее, чем оно могло прослужить. На сегодняшний день основная задача — не переуплотнить слои верхней одежды, но, как показала практика, это довольно проблематично. С данной проблемой помогает справиться плотномер PQI. Стабильность и четкость результатов позволяют четко уплотнять покрытие до требуемых воздушных пустот.
ВЫВОДЫ
Для производства качественных и стабильных асфальтобетонных смесей по ГОСТ 58401 и ГОСТ
58406 требуется:
- использование основных фракций каменных материалов при производстве смеси;
- постоянные испытания битума для определения температуры производства и укладки;
- применение современных асфальтобетонных заводов с пятью-шестью бункерами-накопителями и с точными блоками дозаторов;
- постоянный контроль зернового состава смеси с помощью асфальтоанализатора;
- постоянный контроль максимальной плотности смеси.
Непосредственно на дороге необходимо следить за температурой укладки и контролировать (с помощью плотномера) уплотнение смеси, не допуская переуплотнения. Соблюсти при этом современные жесткие требования позволит только профессиональный подход к выполнению всего комплекса работ.
В статье используются материалы из источника:
http://www.techinform-press.ru/images/stories/pdf/roads100/100.pdf